BACKGROUND
Founded in Germany in 1963, the SANHA Group is the leading European manufacturer of press fit piping systems for water, gas, solar, heating, cooling, and sanitary applications. With an extensive product range comprising over 8,300 products, the SANHA Group operates worldwide and constantly seeks solutions to increase efficiency.
CHALLENGE
The SANHA Group had multiple manufacturing sites working with manual and decentralized work processes. Apart from making it practically impossible to get up-to-date information about delays, identify downtimes, machine errors, and other issues on time, this also made data acquisition very challenging and prevented streamlined workflows, efficient production and critical insights on cycle time.
The Group sought an Industry 4.0 partner to help fully digitize and optimize their production and business processes, and thereby simplify factory floor production, minimize errors across the entire supply chain, and improve production visibility for insightful decision-making. To modernize their entire production process, SANHA needed a solution to connect their existing databases with machines. To enable data retrieval, they needed to connect their IoT devices and smartphones.
SOLUTION
Magic Software’s FactoryEye was selected because it provides an advanced, easy-to-use machine connection, data visibility, and a smart IoT solution for production. Empowering SANHA to take a step towards Industry 4.0 digitization, it automates the end-to-end manufacturing process, identifies machine failures before they happen, detects negative trends early, and provides decision-makers with data in real-time.
“Being able to update our planning system (MRP) in real-time with live production data and finished goods is a major improvement for us. Accurate planning means better scheduling, inventory optimization, and shorter delivery times.”
Andreas Jüsgen, Chief Information Officer
This level of visibility and availability of business-critical data has allowed SANHA to improve factory performance. The entire management team can now view cross-company data on their mobile devices at any time, in any location. Armed with valuable production insights, managers can track production floor issues as soon as they happen and schedule deliveries with increased accuracy, for shortened delivery times.
Connected IoT devices and automated production is turning SANHA into a digital factory, fully prepared with enhanced OTD data to deliver a superior customer experience. Furthermore, visibility and the ability to react and fix issues immediately is a huge gamechanger, because it lowers the reject rate, prevents errors in production, reduces costs, increases available goods, and ensures punctual delivery.
RESULTS
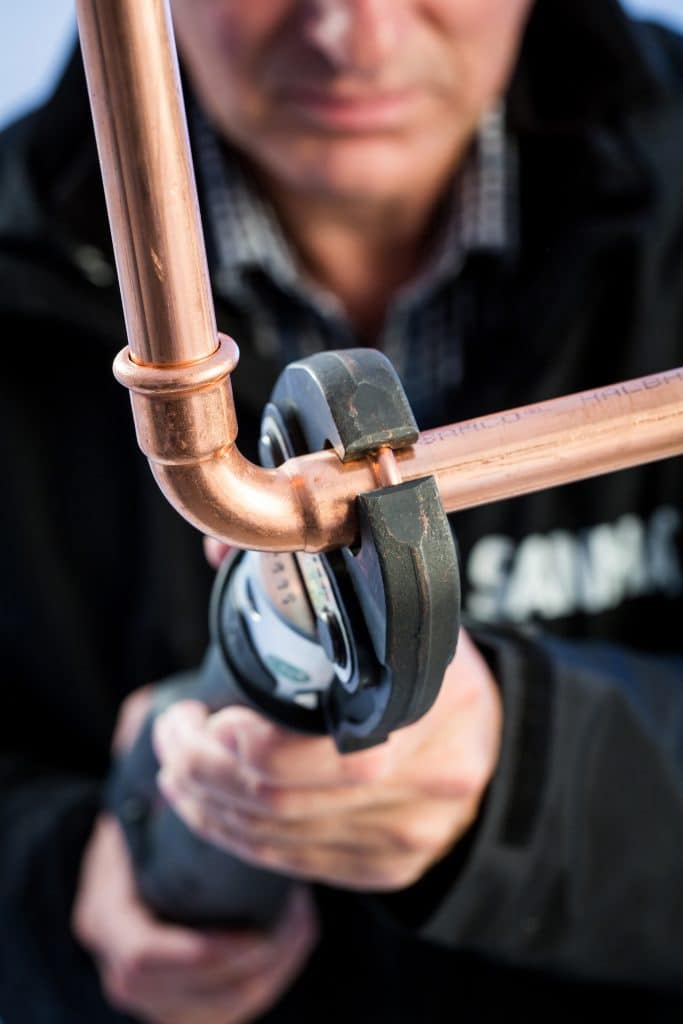
Foto: Udo Geisler
- Smarter and faster responses with real-time data.
- Better productivity with digital processes, allowing machine operators and their managers to focus on the big picture, enhance communication visibility, and be involved in digital change.
- Improved work culture and opportunities for remote work – production and maintenance teams can be on call, rather than on site, during weekends or public holidays.
- Better control over delivery times and inventory management.
- Reduced machine downtime and optimized machine maintenance intervals.
- Lower costs and improved efficiency, productivity, and cost structure.
- Reduction in the number of people required on site, because of the possibility for remote data access, work and collaboration.