Die zunehmende Vernetzung analoger und digitaler Prozesse im industriellen Umfeld stellt Maschinenbau- und Fertigungsunternehmen vor neue Herausforderungen, öffnet aber auch neue Perspektiven der Effizienzsteigerung in der Produktion.
Wie unterstützt Digitalisierung Unternehmen, um in Zeiten globaler Herausforderungen erfolgreich zu bleiben? Wie gewinnen Unternehmen aus Maschinenbau und Fertigung exakte Erkenntnisse aus ihren stetig wachsenden Datenmassen, um die Produktionseffizienz positiv zu beeinflussen? Wie lässt sich die Gesamtanlageneffektivität (GAE) mit digitalen Technologien verbessern?
Erfolgsrelevante Fragen, die Unternehmen umtreiben. Wir fragen bei Michael Kügeler von Magic Software nach. Er ist Experte auf dem Gebiet der Digitalen Transformation und unterstützt Unternehmen in Fragen rund um geeignete Lösungsarchitekturen, Portale, Prozessanalysen und Automatisierung.
Herr Kügeler, im Zusammenhang mit der industriellen Produktionsplanung fällt immer wieder der Begriff Gesamtanlageneffektivität, kurz GAE. Was bedeutet das genau?
„GAE“ ist eine Kennzahl in der Produktion und steht für Gesamtanlageneffektivität, im Englischen gleichbedeutend mit OEE (Overall Equipment Effectiveness). Sie verdeutlicht die Wertschöpfung einer Anlage, indem sie ihre Produktivität ins Verhältnis zu Faktoren stellt, die die Produktivität beeinflussen.
Die Methode ist zunächst ein allgemeiner Ansatz. Im Zuge der Digitalisierung und aufgrund verfügbarer Maschinendaten in Echtzeit ist er jetzt wesentlich aussagekräftiger anzuwenden als mit herkömmlichen Mitteln.
Welche Faktoren sind dabei relevant?
Die Kennzahl ergibt sich aus dem Vergleich der tatsächlichen mit der potenziellen Verfügbarkeit, Leistung und Qualität einer Anlage. Das Erfassen und anschließende Multiplizieren der drei Faktoren führt zur GAE. Wichtige Aspekte sind geplante und kurzfristige Stillstände, Pausen, Störungen, Rüstvorgänge, verringerte Geschwindigkeiten und die Menge der einwandfrei produzierten Waren in Relation zum Ausschuss.
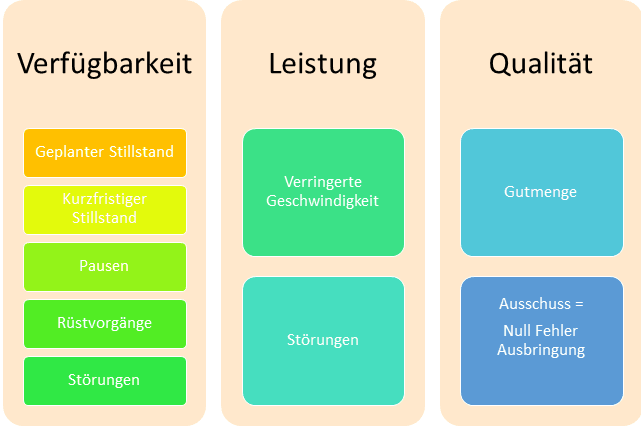
Gesamtanlageneffektivität (GAE)
Wie berechnet sich die Gesamtanlageneffektivität (GAE) konkret?
Der GAE Quotient ergibt sich aus der Gesamtstückzahl abzüglich des Ausschusses geteilt durch die Gesamtstückzahl. Aufgeschrieben sieht das wie folgt aus: QR = (Gesamt – Ausschuss) / Gesamt.
Welche GAE – Messwerte dienen Unternehmen als Orientierung?
Ein GAE-Messwert von 100% steht für eine perfekte Produktion und bedeutet: Es werden nur einwandfreie Teile hergestellt und dies zeitlich und ohne Unterbrechungen wie in der Planung vorgesehen. Praktische Erfahrungen in unterschiedlichen Industrien zeigen, dass ein GAE-Messwert von 85% ein Spitzenwert ist. Die durchschnittliche GAE für Produktionsstätten beträgt weltweit allerdings ungefähr 60 %. Das bedeutet, dass noch erheblicher Verbesserungsbedarf besteht.
Wie lässt sich die Gesamtanlageneffektivität (GAE) mit digitalen Technologien verbessern?
Ein treibender Faktor der Digitalisierung ist das Internet der Dinge. Technologien und Konzepte, die heute mit dem Begriff IoT (Internet of Things) umschrieben werden, ermöglichen erweiterte und neue Möglichkeiten der Automatisierung und Datenerfassung. Aufgrund vernetzter Geräte und Maschinen aller Art werden Daten in einem bisher nicht bekannten Umfang gesammelt und ausgewertet. Darauf aufbauend lassen sich Daten für die Berechnung der GAE verwenden, die im Rahmen der Produktionsprozesse generiert werden. Bezüglich der Methodik ist ein strukturiertes Vorgehen in mehreren Phasen empfehlenswert, wobei diese als automatisierte Endlosschleife während der Produktion ablaufen.
Wie sehen diese Schritte praktisch aus?
Der erste Schritt umfasst das Einbinden möglichst aller vorhandenen Datenquellen im Unternehmen. Es gilt, die einzelnen Datensysteme miteinander zu vernetzen und Datensilos zu vermeiden. Im Rahmen der Datenerfassung erfolgt im zweiten Schritt eine strukturierte Datenaufnahme.
Die folgenden Schritte lassen sich unter dem Oberbegriff „anwendungsgetriebene Datenanalyse“ zusammenfassen: Verantwortliche Personen erkennen und verstehen ein bestehendes Problem und formulieren einen Anwendungsfall. Es folgt das Aufbereiten und im Anschluss die dezidierte Analyse der Daten. Der nächste Schritt besteht aus zwei Teilschritten: das Implementieren der Daten in ein Modell und die darauf aufbauende Visualisierung.
Der letzte Schritt umfasst die Anwendung der erzielten Erkenntnisse aus den vorhergehenden Schritten im Produktionsprozess. Der Ergebnisrückfluss erlaubt Rückschlüsse und diese tragen zu einer verbesserten Gesamtanlageneffektivität (GAE) bei.
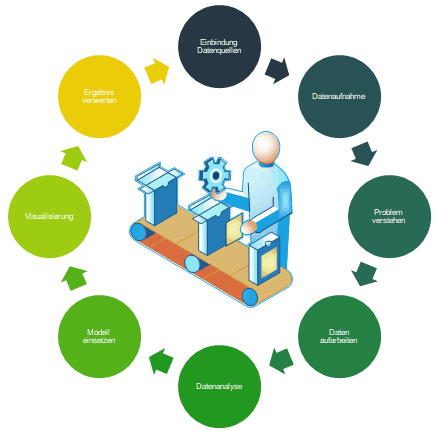
Schrittweise zu einer verbesserten Gesamtanlageneffektivität (GAE)
Welche Rohdaten liefern Sensoren?
Mit Hilfe von Sensoren lassen sich zahlreiche Rohdaten zu unterschiedlichsten Messgrößen abrufen. Dazu zählen Temperatur, Durchfluss, Kraft, Beschleunigung sowie Schall, Position, Abstand und der Füllstand bei Flüssigkeiten. Bild- und Farbsensoren können Objekte erkennen und in ihrem Verhalten beobachten.
Wie sieht es mit älteren Maschinen aus, die über keine Sensoren verfügen?
Ein kompletter Austausch des Maschinenparks ist nicht unbedingt notwendig. Sensoren lassen sich in bestehende Maschinen einbauen oder mithilfe bestimmter Komponenten erweitern. Mittlerweile gibt es zum Beispiel Lösungen auf Basis von Raspberry PI oder Arduino, die sich in bestehende Anlagen integrieren und als Datenquelle verwenden lassen.
Welche projektbezogenen Aufgaben sind am zeitintensivsten?
Im Durchschnitt erfordert die Aggregation der Daten den höchsten Zeitaufwand, da sie aus vielfältigen Quellen kommen und teils unstrukturiert aufgenommen werden. Das eigentliche Erfassen und Sammeln ist ebenfalls aufwändig, da zunächst relevante Datenquellen identifiziert werden und dementsprechend Speicherkonzepte aufgebaut werden müssen.
Wie können Integrationsplattformen bei der Projektumsetzung helfen?
Mit Integrationslösungen lassen sich bei Bedarf Daten aus unterschiedlichen Systemen über eine Datendrehscheibe abrufen und miteinander verknüpfen. Die für die Ermittlung des GAE benötigten Daten werden zusammengeführt, egal wo sich die Daten innerhalb der Wertschöpfungskette befinden. Umständliche Techniken wie manuelle Synchronisation oder Kopieren zwischen den Systemen entfallen. Unternehmen erhalten maximale Flexibilität.
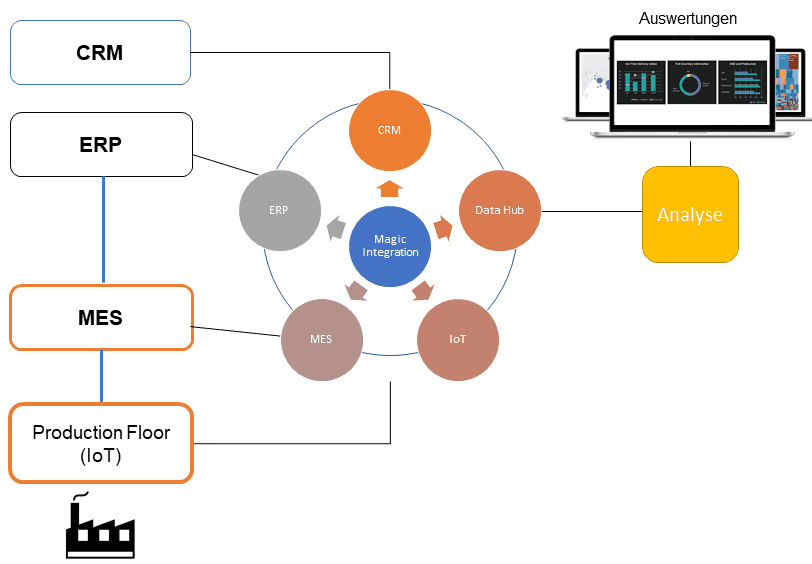
Integrationsplattformen unterstützen den Digitalisierungsprozess
Welche Vorteile ergeben sich konkret für die Produktion?
Integrationsplattformen können entscheidend zu einer gesteigerten GAE und einer optimierten Auslastung der Anlagen beitragen. Sie unterstützen eine bedarfsgerechte Materialversorgung und ermöglichen vorausschauende Wartungszyklen, im Englischen auch Predictive Maintenance genannt.
Stichwort Predictive Maintenance: Wie profitiert ein produzierendes Unternehmen in der Praxis?
Konkret lassen sich eine höhere Anlagenverfügbarkeit sowie eine verbesserte Produkt- und Prozessqualität im Fertigungsprozess erzielen. Servicezyklen werden transparenter und der Koordinationsaufwand mit Servicedienstleistern sinkt. Anlagen sind weniger reparaturanfällig, benötigen weniger Ersatzteile und laufen länger. Predictive Maintenance erhöht die Betriebssicherheit und Nachhaltigkeit.
Was geben Sie produzierenden Unternehmen mit auf den Weg?
Aufgrund historisch gewachsener Systemlandschaften im Fertigungsumfeld stehen viele Unternehmen vor der Herausforderung, bestehende aber nicht unbedingt effiziente Systeme im Kontext der Modernisierung neu zu betrachten. Früher oder später stellt sich die Frage, wie alte und neue Systeme im Sinne einer zukunftsorientierten Lösung aufeinander abzustimmen sind.
Ich empfehle Unternehmen, die sich mit digitaler Transformation auseinandersetzen, bereits in einer frühen Phase systemübergreifend zu denken und sich nicht nur einzelnen Anwendungen zu widmen. Eine systemübergreifende Integration ermöglicht es, Daten aus bestehenden Quellen und neuen Datenplattformen mit Hilfe von Cloud-Diensten umfassend aufzunehmen.
Als langjähriger Integrationsspezialist auf dem Markt bieten wir Unternehmen aus Produktion und Fertigung moderne und flexible Lösungen an und setzen diese – wahlweise mit der hausinternen IT-Abteilung oder mit einem erfahrenen Partner – um.
Herr Kügeler, wir danken Ihnen für diese ausführlichen Informationen.
Gemeinsam mit Channel Partnern unterstützt Magic Software Unternehmen bei der Digitalen Transformation. Weiterführende Informationen über Integrationslösungen für die Produktion erhalten Sie auf der Unternehmenswebseite.
Ein Integrationsbeispiel aus der Produktion sehen Sie in dem Video der Aerzener Maschinenfabrik. Die Aerzener Maschinenfabrik GmbH konstruiert seit 1864 AERZEN Hochleistungsmaschinen für die Industrie und hat sich von einer reinen Maschinenfabrik zu einem Global Player entwickelt.
Channel Partner aufgepasst! Bei Interesse an einer Partnerschaft mit Magic Software finden Sie das Partner Integration Programm zum Nachlesen auf der Webseite.
Für Fragen steht Ihnen Michael Kügeler über unser Kontaktformular oder telefonisch unter +49 (0)89 96273-0 sehr gerne zur Verfügung.
Bildnachweis: Pixabay